
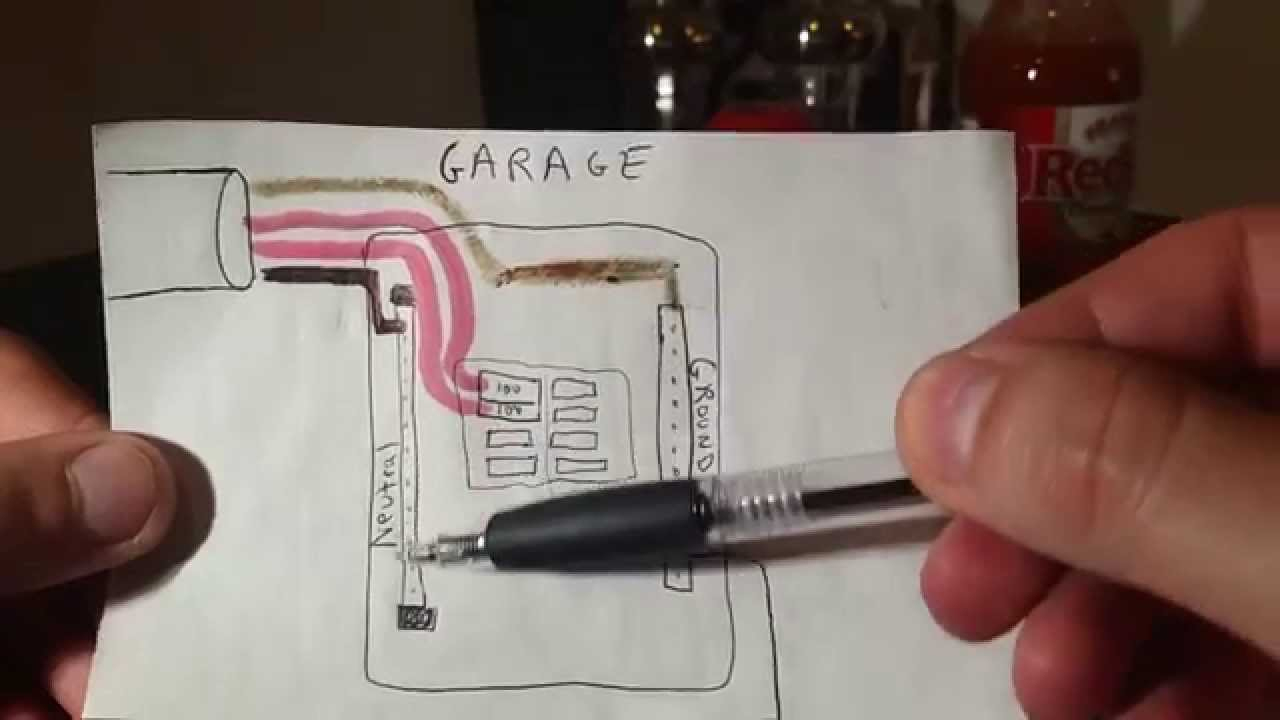
So a "24/48" panel is actually 24, period. Those are useless as almost all new work today requires GFCI, AFCI or both - and you cannot obtain those in double-stuff. What doesn't work is "double-stuff" breakers (including GE's 1/2" Q-line breakers). GFCI and AFCI breakers are available for them. You can also look at the CH or QO panels, which use 3/4" high breakers, so more spaces in the same panel footprint. Voila, no breakers needed, space maximized! If so, order a main panel with thru lugs, which will save 2 breaker spaces, and a 125A sub.
#SERVICE WIRE FOR 100 AMP PANEL UPGRADE#
See if you can upgrade the main-sub cable to 125A. Even if not, you can order a 125A main panel and swap the main breaker to 100A. Talk to the power company and see if your service drop/meter can support 125A. With that in mind, back to replacing the panel(s). You can use thru-lugs or snap-in lugs in the main panel. If the main panel is breakered at 100A, and the cable supports 100A, and the subpanel supports 100A, then the main main breaker protects them all. At the subpanel, the cable/wire can land on main lugs (provided the subpanel is rated for 60A+) or on the subpanel's main breaker (of any rating - a smaller main protects the panel, a larger main is just a shutoff switch, which you do not need since it's in the same building.) So if the subpanel has main lugs, use them instead of backfeeding a breaker. A 60A breaker is correct to protect #6Cu or #4Al. It needs a breaker upstream (in the main panel) to protect the cable. The cable between main and sub doesn't need 2 breakers. Brand X breaker won't engage Brand Y buses with the correct contact shape or clamping force, causing the arcing. The #1 cause is using the wrong brand of breaker. Catch it early and you may be able to save the breaker space, otherwise that's a dead space in your panel. Likewise corrosion (read: arcing) on breaker contact points is absolutely unacceptable. Many electricians in the 80s and 90s did not get the memo.

Fix immediately! Aluminum feeder wire is fine stuff, but you do need to use the anti-ox goop, and torque it correctly. This one popped up for some reason, so I'll edit in some new thoughts.Ĭorroded or arcing power feeds are "burn your house down" serious business. Is there any limit to the number of tandem switches that can be used in one of these panels (e.g., Square-D HOM2448M125PC)?.Does going from a 100 AMP to a 125 AMP panel require any change in the gauge of the wire coming from the meter?.I can also reduce the number of breaker spaces I need by consolidating circuits (LOTS of the interior outlets are direct runs to the panel, there's no reason the LR, for example, can't all be on one breaker instead of 3), and by using a few tandem breakers. I can get the same footprint Square-D panel with either a 100 AMP or 125 AMP main breaker. I don't have a lot of vertical space to go with a 200 AMP panel with a lot of spaces. The primary panel has a 100 AMP main breaker, connected to the meter outside.Īside from this thing being a monstrosity, the "subpanel" has corrosion in spots on some of the breaker contact points, reducing voltage to 108 or so on some circuits (diagnosing why some things worked and others didn't when plugged into certain outlets was a multi-day adventure.) The thing that just pushed me into action is that the screw-downs for the feed from the meter on the 100 AMP breaker are corroded, and one is actually loose and occasionally arcs. There are two Square-D 22? space panels wired to each other, with one being a subpanel with a 60 AMP link from the primary one (there is a 60 AMP breaker in each panel that are linked together with some super-thick aluminum braided wire). My house currently has a mess of a load center setup that I need to correct. I took a look at some of the other threads, but none seemed to give me a clear answer:
